Adapted from this SLAC press release
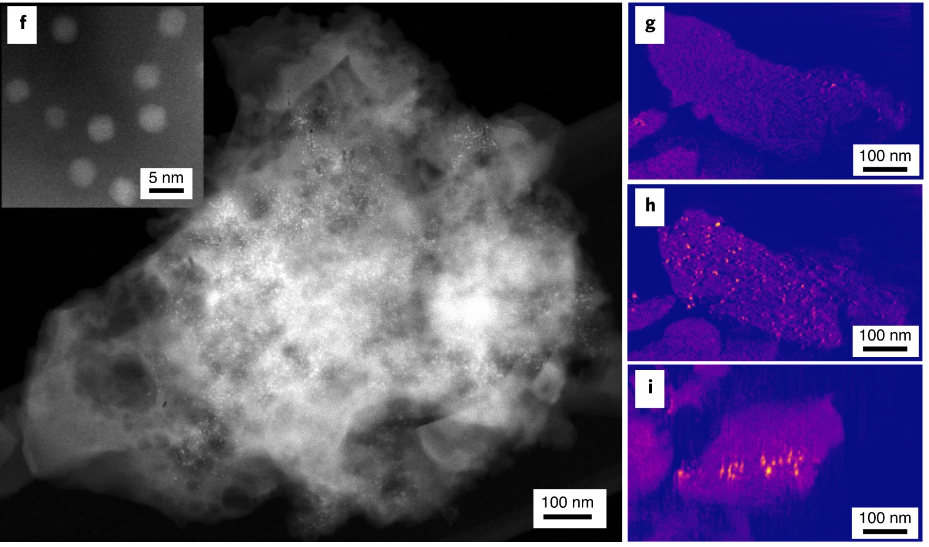
Sometimes, solutions to environmental problems can have environmentally unfriendly side effects. For example, while most gas-powered cars have a catalytic converter that transforms engine emission pollutants into less harmful gases, this comes with a tradeoff: Catalytic converters contain precious metals such as platinum and palladium.
The good thing about these precious metals is that they act as catalysts that help break down pollutants, with a suite of properties that make them the best elemental candidates for this chemical job. But they are also rare, which makes them expensive, and extracting them from the earth produces its own pollution.
However, in a paper published October 24 in Nature Materials, Foundry staff, along with users from Stanford University and the Department of Energy’s SLAC National Accelerator Laboratory, reported a way of encapsulating catalysts that could reduce the amount of precious metals catalytic converters need to work, which could in turn reduce the practice of precious metal mining.
The inside of a catalytic converter is hot, steamy, and filled with oxygen. This might sound nice, but it’s actually a harsh environment that deactivates precious metal catalysts.
As soon as someone drives a car, the nanoparticles of catalyst present in the catalytic converter are exposed to high temperatures that cause them to coalesce and form larger particles. This process is known as sintering, and these bigger, sintered chunks of catalyst mean less overall active surface area for the catalysts to do their job: the larger the particles, the lower the catalytic efficiency.
Car manufacturers must use a certain amount of catalyst to keep a catalytic converter at the required level of efficiency. But if a catalyst were to be resistant to sintering and deactivation, car manufacturers could use less precious metal.
The research team came up with an idea for a catalyst system that can do just that. They built a nanoscale alumina framework to encase catalyst nanoparticles – in this case, the precious metal platinum.
The team produced this cage with nanocasting: They first sandwiched platinum nanoparticles between porous layers of polymer, then filled the pores with alumina. After burning away the polymer mold with heat, they were left with a web-like cage of alumina surrounding the nanoparticles.
Interested in Becoming a Foundry User?
Join our collaborative, multidisciplinary environment.
Learn more >
Alumina is a ceramic, like a coffee mug, so it’s rigid enough to keep the nanoparticles in place. But it’s also porous, so there are openings in the framework where the surface of the nanoparticles can carry out reactions.
The team used X-rays produced by the Stanford Synchrotron Radiation Lightsource (SSRL) at SLAC to conduct X-ray absorption spectroscopy on their samples, which revealed the size of the platinum nanoparticles. These sensitive X-rays were able to examine the small amounts of platinum. SSRL also allowed the team to study the sorts of tumultuous reactions that take place in a catalytic converter.
They also used electon microscopes at the Foundry’s NCEM facility to fully characterize the material at the atomic scale.